WM President and Chief Operating Officer John Morris remembers driving his first waste vehicles in college, a time when riding on the back of the truck was standard and “the only air conditioning was rolling the windows down.”
Today, Morris oversees field operations for the company, which has a fleet of over 18,000 collection vehicles and a suite of technologies to make those vehicles safer and more efficient. “The technology that's in these trucks is light years ahead of where it was,” he said.
Morris was appointed president of WM last week. He’ll continue his field operations role, and multiple executives, including those leading sustainability, customer experience and enterprise strategy, will now report to him. Morris has previously served as market area general manager of New York City, area vice president of the greater Mid-Atlantic Area, chief strategy officer, and senior vice president of field operations.
Morris says the company has been strategic about how it adopts and rolls out the latest tech upgrades. The industry struggles to retain labor, he said, and the right investments are helping WM become less labor dependent. At the same time, it also provides opportunities to retain employees by providing vehicles and facilities that are safer and more comfortable than before.
“When we buy more expensive, sophisticated trucks, it costs more to maintain them, but the overall benefit to the business is something we’re comfortable with,” he said. “First and foremost, I want to be safe. But we're also in business to be profitable, not just efficient.”
Morris sat down with Waste Dive on May 6, during WasteExpo in Las Vegas, to discuss how WM is adding AI upgrades to its existing technology, improving on longtime cab technology and piloting new programs for heavy equipment operators. He also discussed pilot programs for using autonomous vehicle technology at landfills. WM CEO Jim Fish has previously called for a “significant percentage” of WM’s heavy equipment fleet be autonomous by 2030.
This conversation has been edited for length and clarity.
WASTE DIVE: AI has become an important element of equipment and fleet improvements in the industry, and it’s been a big topic of conversation at WasteExpo. What’s new on that front for WM?
JOHN MORRIS: AI is helping inform the business better and helping us operate more efficiently. We’ve had forms of artificial intelligence in the business for probably eight or 10 years.
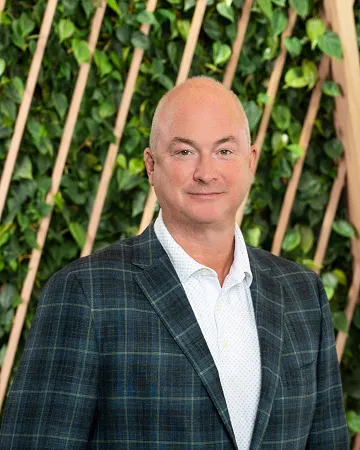
If you go into our recycling facilities, what was once a manual sorting role has been automated over the years. When you look at those optical sorters, that is a form of artificial intelligence. It's reading the material and sorting without us ever having to touch it. AI is also helping us from a safety perspective to avoid things like repetitive motion injuries, as well as from an efficiency standpoint.
When you look inside some of our cabs, it’s interesting to see why [we first adopted AI-assisted technology in trucks]. We had a very prohibitive labor agreement on the West Coast [about 15 years ago], and we were having a problem with our drivers taking pictures if the cans were overloaded. They were supposed to take a picture and send it to a mailbox so we could send the sales rep out [to talk to the customer.] We could not get folks in that particular labor union under that labor agreement to take pictures.
We started looking for ways to augment what they wouldn't do by using technology. What that has morphed into is now every one of our commercial front-load trucks gets still or video images of every transaction.
When we service a container, we can see what's happening as we're going into the container, both the outside and what's inside, and we have cameras on the hopper. We probably pick up about 700 million yards a year of commercial material. That gets us data on every one of those transactions, so you really start to understand customer behavior to see what’s working, not working, or you can address safety issues.
Virtually none of those images are processed by a person. There's still a human in the loop, but it’s more of a [quality control] thing. We have a team in India, and if we have to send [an image] to somebody in operations or sales, that information will come back overnight, so there's a lot of power in that.
The other area where I've been thrilled with the progress we're making is really from a safety perspective. We were an early adopter of Lytx [a fleet management and telematics technology]. We have that technology in every one of our collection vehicles and all our supervisory vehicles.
We've been using artificial intelligence and recognition technology to be able to identify [potentially unsafe driving behavior]. That information, gathered through AI, is coaching people in a positive way, as opposed to disciplining them.
It's so hard to hire drivers. So when we look at that technology, we see a coaching opportunity and a development opportunity. You can sit down with one of your drivers and say, “Hey, listen, here's what we've been noticing about your behavior. You should be following at three seconds, because if you don’t, you're 40% more likely to have a collision.”
Like a lot of other haulers in the industry, WM has also been working on its route optimization process. What’s the priority there?
We've had routing engineers and different forms of routing software. Everybody in the industry has for a lot of years, but there was really never a software program that was built specifically for the waste industry. With the number of transactions we do a year, certainly, we want to make sure that our folks are efficient. We also found that when you have “routine breakers,” meaning you have to deviate from a schedule for some reason, the risk of having an incident goes up.
We run about 4,000 industrial roll-off routes. How we route on Monday is entirely different on Tuesday. So there's a dynamic nature in that industrial line of business that's unique — more so than commercial, and certainly more so than residential. We saw the opportunity to build out an [industrial] routing technology through our internal ops research team. The key is that it's dynamic. There are about 72 attributes that go into making a decision on how to service an industrial roll-off container, things like container type, truck type, disposal type, location.
We just made another improvement that we're rolling out. We've had tablets in our trucks and onboard computers for over a decade, but when you pull up to a container, drivers have to [interact with the screen multiple times]. What we're trying to do is find ways to make the technology passive. … We want them to focus on safely servicing their customers and not get distracted. So we went back with our software engineers and reworked it so that now we'll use the latitude and longitude of the truck and actuators on the arms to be able to automatically confirm that we've serviced the container.
What’s the overarching strategy for WM when it comes to budgeting for and integrating these kinds of tech and AI improvements? Where do the labor considerations come into play?
I often talk about total cost of operation. [For example,] we have more sophisticated trucks now, with a lot more technology, so they're going to be more expensive to maintain. I'm more interested in knowing the total cost of operation.
We can look at how we allocate dollars on capital, and what we've been cautious about is making sure that we're not putting technology in for technology's sake. When you talk about AI, it means 50 different things to 50 different people. I talk about it in terms of, how are we going to use technology broadly to modernize our business model and structurally get our cost down?
Even though the pressure on the labor market has eased from where it was a few years ago, I think over the long term, if you sort of follow the math, those labor scarcity issues are going to persist. I sit on the board of the National Association of Manufacturers, and there are stats [from that business sector] that say in the next five years we're going to need 4 million folks to fill manufacturing jobs. We'll be lucky to get half of them.
Do you think autonomous vehicles will be part of the equation soon?
There’s something we are piloting right now [in Arizona and in the Pacific Northwest]. We've done some work with some heavy equipment folks on remote control operations.
If you have a facility in the middle of nowhere, a very hard-to-access place, it's gonna be hard to get labor. However, maybe you can put someone in a chair in what looks like a gaming room, they can run the equipment from anywhere. That certainly is going to help from a labor perspective. An example could be automating operations like [loading dirt at a landfill].
Heavy equipment is probably a near-term application for those reasons. I could see an application where we might be able to do some form of autonomous movement of long-haul waste. But are we right around the corner from having a fully autonomous refuse vehicle running through neighborhoods and school zones? I think that [will take longer].
As far as labor training, we've had training centers for years, and we train about 85 to 90 drivers every week and about 15 to 20 technicians every week. We are just now rolling out the [program] for heavy equipment operators. Our training facility in Florida is on a closed landfill, so it's an ideal spot for heavy equipment operators.
We are going to continue having labor scarcity and facing the cost of labor, and we continue looking to the advancement of technology [to help] outstrip that labor pressure. At the same time, everybody in the industry is trying to figure out how to hang on to their employees.