This story is the first in a series about chemical recycling’s impact on the waste industry, commodities and policy.
Chemical recycling is at a turning point in proving its financial viability and ability to scale to meet the demands of a changing plastics recycling industry.
Years ago, many of the technologies that make chemical recycling possible were still in the developmental stage, with companies focusing on getting their work out of the lab and into the real world.
But now companies such as Dow, Eastman, LyondellBasell, ExxonMobil, PureCycle, Cyclyx, and others are investing millions of dollars a year in scaling those technologies, saying the investments will speed up the process of keeping hard-to-recycle plastics out of landfills and funnel them into feedstocks for new products.
Chemical recycling, also called advanced recycling or molecular recycling by the plastics industry, is a broad term for numerous processing technologies that break down recovered plastics to the molecular level to become “building blocks” for new plastics or other products. Common techniques include pyrolysis, gasification and depolymerization.
Companies have poured millions of dollars into expanding capabilities in recent years, and they say those investments are finally paying off as they move on from small-scale experiments and open new facilities or ink offtake agreements. Mechanical recyclers and waste companies are also getting involved. Meanwhile, recently passed laws could make it easier to open facilities in certain states.
But some environmental and health experts say chemical recycling companies aren’t able to manage the volumes of material they claim, fueling an unsustainable reliance on plastic instead of taking steps to reduce or eliminate plastic use. They also worry the facilities create harmful health impacts.
Over the past year, Waste Dive has spoken with numerous waste and recycling experts, researchers, lawmakers, companies and other stakeholders to learn how chemical recycling will continue to affect the industry.
The fight over chemical recycling is playing out in almost every corner of the industry — from regulations and job creation to investments and commodity markets. Industry players say the next few years will determine just how embedded chemical recycling will become in the overall recycling landscape, and whether numerous companies’ scale-up plans will reach commercial scale significant enough to fulfill their promises.
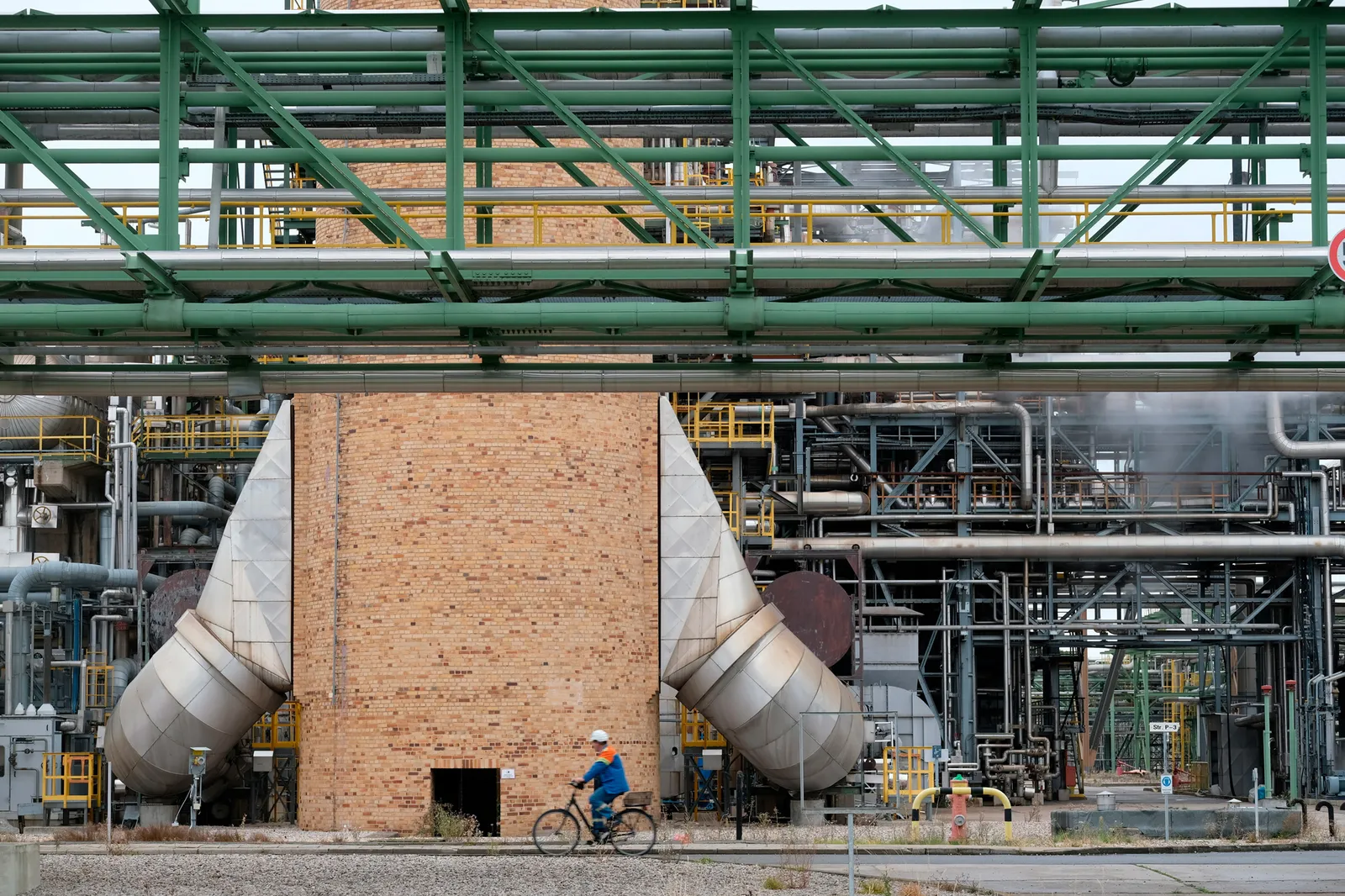
A tale of scale
The fight comes as the plastic recycling rate has stagnated in the U.S., and lawmakers and local recyclers are pushing for more and better recycling infrastructure. At the same time, the public is putting more pressure on major brands to use more recycled content, prompting companies to make public recycled content goals they’ll need to meet by as early as 2025.
A coalition of major brands has called for access to up to 800,000 metric tons of chemically recycled plastics by 2030. The international community is also eyeing how chemical recycling could play a role in global plastic pollution management. The UN is working on an international legally binding agreement on plastic pollution, and treaty discussions have touched on how stakeholders see chemical recycling’s role either as a potent way to process plastic trash and as a “dangerous practice.”
Rather than position themselves as rivals to the existing recycling industry’s mechanical sortation and processing, chemical recyclers are selling themselves as an important partner in turbo-charging waste diversion and recycling. Chemical recycling can accept some lower-value mixed plastics mechanical recyclers aren’t interested in, they say. The processes can take in numerous colors of plastic — including colors that sometimes have limited markets, like black — and filter out the dyes as part of the process of breaking them down to the monomer level.
“If you look at the issue that we have in front of us, which is the challenge of plastic waste, it requires some really innovative solutions, but especially solutions that can give you scale because of the scale of the challenge,” said Manav Lahoti, Dow’s global sustainability director for Hydrocarbons and Business, in an interview late last year. “Mechanical recycling is an important component, but it doesn't allow you to recycle these plastics at scale. That’s what advanced recycling does.”
Many major chemical recycling announcements in the past two years have focused on scale. That includes announcements of building new or bigger facilities, as well as announcing strategic partnerships and offtake agreements.
Paschalis Alexandridis, a professor at the University of Buffalo’s Department of Chemical and Biological Engineering who studies plastics recycling, says “scalable” is an important buzzword that defines the turning point of chemical recycling today. Numerous university researchers are working on chemical recycling technologies at the lab level and are looking to connect with companies to scale the findings into full-blown commercial solutions.
Millions of pounds of plastic produced each year, and just a small percentage of it recycled in the U.S., Alexandridis said during a presentation at the REMADE conference, an academic event focusing on the circular economy, in March.
“Some people say the solution is to get rid of plastic or come up with some kind of magic chemistry — but each of those ‘solutions’ cannot handle [that many] pounds of plastic a year. There's no way. As a result, we need many different approaches, and need them soon.”
Consumer and brand pressure, mixed with recently-passed recycled content laws in places like California, are big policy drivers that have created an environment for advanced recycling projects to really take off, said Haley Lowry, Dow’s global sustainability director for packaging and specialty plastics, in an interview late last year.
Dow announced last year it would “commercialize 3 million metric tons of circular and renewable solutions a year” by 2030, using plastic waste and “other forms of alternative feedstock” to create new products. The company’s previous target had been 1 million metric tons a year.
“To do that, that's not just going to be mechanical recycling. It's not just going to be advanced recycling. That's not just going to be biobased materials,” Lowry added during a presentation at the Plastics Recycling Conference in March. “We really are looking at a suite of technologies to put forward, and advanced recycling is a critical part of our strategy.”
To do that, Dow is building chemical recycling facilities and investing in mechanical recycling sites and hybrid sites, as well as entering into new agreements with companies to process plastic waste.
ExxonMobil is another company investing millions in its efforts to scale chemical recycling technologies. One major project is a 40,000 ton-per-year chemical recycling facility in Baytown, Texas, part of its goal to build approximately 500,000 metric tons of collective advanced recycling capacity across the U.S., Canada, Europe and Asia by the end of 2026.
Natalie Martinez, ExxonMobil’s North America advanced recycling commercial manager touted its expansion plans during the conference. “Something that's really important for us — and what we think is important for the industry — is to be able to do this at scale to really create a very meaningful solution,” she said.
Meanwhile, Eastman Chemical has touted its molecular recycling facility in Kingsport, Tennessee, expected to have a capacity of 100,000 metric tons at full build-out, and is also looking to build two additional facilities: one in a yet-to-be named American city and one in France.
The plant was originally expected to open in 2022. Eastman executives said in prepared remarks during its Q2 earnings call in July that it has recently made “substantial progress improving the pace of construction over the last several months, although ramp up took a little longer than we wanted.” Its pilot plant, meanwhile, has been “operational for over two years, which has enabled continuous improvement in the technology.” Eastman aims to produce material from the pilot by the end of the year.

Teaming up with mechanical recycling
A major part of chemical recycling companies’ messaging is that they aren’t out to compete for materials with stable recycled commodity markets, like PET bottles and HDPE jugs.
“We're focused on streams that do not have good options or good homes within mechanical recycling,” said Holli Alexander, director of sustainability for specialty plastics at Eastman, during a session at the Plastics Recycling conference earlier this year. “We want to expand the pie.”
Major recyclers like WM also see opportunities for the two technologies to work alongside one another. The company has partnered with Dow on a pilot project in the Chicago area to collect plastic film in their curbside bins. WM says the pilot program could help them divert more than 120,000 metric tons of plastics film from landfills each year of the project. Both mechanical and chemical recycling processes could be used to convert the material.
“I think there is still a heavy demand for chemical recycling facilities in the U.S., because naturally, mechanical recyclers can't take everything,” said Brent Bell, WM’s vice president of recycling, at the conference.
That plastic film is a feedstock ideal for Dow’s chemical recycling processes and is not commonly recycled by WM. Bell says it’s an example of increasing industry agreement that chemical and mechanical recycling operations want different kinds of material and can work together to move it to the right homes.
“You'll hear from most everybody, whether you're on the chemical or mechanical side, that mechanical recycling should always get first priority” on recyclable material. “Even the big chemical recycling backers tell us that,” he said.
The Houston Recycling Collaboration is another example. The City of Houston, along with FCC Environmental Services, ExxonMobil, LyondellBasell and Cyclyx, established the group in 2022 to raise the city’s plastic recycling rate and scale up both mechanical and chemical recycling business by collecting all types of plastics throughout the city. The collaboration is working on several projects, including a program expanding the materials accepted for recycling at 10 of the city’s recycling drop-off locations. By the end of they year, the group aims to allow residents to drop off all types of plastic, including dry cleaner bags, bubble wrap and Styrofoam.
The difference in operating costs between mechanical and chemical recycling facilities could also ease competition for some types of plastic both operators might want in the future, said Will Sagar, executive director of the Southeast Recycling Development Council.
“We don't feel threatened by advanced recycling because it is going to have an operational cost that's significantly higher than mechanical recycling, so they're not going to be willing to pay the same amount for a bale,” he said. “The mechanical recycler still has the competitive advantage to use the good material.”
However, as more chemical recyclers enter the picture, their preferences could influence the commodities market, Sagar added. “It may bring about a floor price for bales to provide some stability, because if PET or HDPE bales fall below a certain price, at that point, it becomes doable for the advanced recycled community to start buying. But [at a time when] clear HDPE is worth more than cans, it’s not so likely.”
Legislative policies make room for chemical recycling advancements
As major companies continue focusing on investments and operations, chemical recycling proponents are trying to clear the way for such businesses to operate more easily by passing state and federal legislation reclassifying chemical recycling as a manufacturing process instead of waste management.
An influential player in this sphere is the American Chemistry Council, which has helped pass at least 24 state bills in the last few years. All but one of those bills passed in states with a majority-Republican legislature.
Supporters say the reclassification can help bring new business to the state and possibly boost state recycling or waste diversion goals. At a Senate subcommittee hearing in March, Sen. Markwayne Mullin, R-Okla., called for further investments in advanced recycling, saying the technologies are in the spirit of American innovation and job creation.
It’s not the first time chemical recycling became the subject of a Congressional hearing in the last year, a sign that the technologies are gaining more attention on a national scale. Meanwhile, some House Republicans have advocated for more research and resources for chemical recycling technologies.
Yet environmental groups have pushed back against the bills, saying the classification will help the facilities skirt environmental permitting or regulatory efforts. Last year, the Rhode Island legislature killed a similar bill, due in part to significant criticism from environmental groups. ACC has said that even when such facilities are regulated as manufacturing instead of waste management, most must meet Clean Air Act and other emissions rules.
In Illinois, the introduction of a bill in March highlighted larger tensions over the role regulations could play in facilities permitting at the state level. The bill, which failed to pass, would have extended the timeline for an unnamed chemical recycling facility to start construction — a move supporters such as petrochemical groups said would have helped along a project hampered by supply chain and COVID-19 delays. Several environmental advocacy groups said the bill would have allowed the facility to sidestep important environmental regulations.
Chemical recycling discussions are also showing up in other types of state bills, including extended producer responsibility discussions. Some argue that chemically-recycled plastics should be counted toward EPR targets in states with forthcoming programs.
On the federal level, several Democratic lawmakers have sponsored legislation meant to make transitioning away from plastics a priority. The Protecting Communities from Plastics Act, introduced in Congress late last year, called for tighter plastics manufacturing industry regulations, including a temporary permitting pause for some facilities, including some considered to be chemical recycling facilities.
Unanswered questions
The industry has big ideas, but lingering environmental questions and regulatory uncertainty could create a possible drag on scaling up the business aspect of chemical recycling’s future.
Federal regulators have yet to weigh in on how or where chemical recycling may be allowed to grow. In 2021, the U.S. EPA opened a formal rulemaking process to determine how to regulate pyrolysis and gasification units, which currently are classified as waste combustion under the Clean Air Act.
The EPA said a more in-depth look was needed because of “considerable confusion” about which operations it should manage under such regulations, particularly due to public questions about the technologies’ role in plastics processing. Environmentalists say the regulation should stay as-is, but the plastics industry says the pyrolysis and gasification designations don’t apply to most kinds of chemical recycling. It’s unclear when a draft rule will be released, and an EPA spokesperson did not respond to questions as of press time.
For some environmental groups, federal and regulatory action on chemical recycling is a necessary step in preventing more plastics-related industries from scaling up to the commercial capabilities they advertise.
Groups like the Sierra Club and the Global Alliance for Incinerator Alternatives see chemical recycling projects as greenwashing, and believe companies like ExxonMobil, Dow and others hype up circular economy strategies and recycling solutions in order to make more plastic without proper scrutiny from regulators. This runs counter to activists’ beliefs that reducing or eliminating plastics is the solution to pollution issues.
Sirine Rached, GAIA’s plastics policy coordinator, said ongoing U.N. global plastics treaty negotiations have shed light on petrochemical companies “dubious” marketing. “Governments are finally awakening to the reality that these technologies are neither innovative nor safe, and that more toxic and carbon emissions are the last thing we need when it comes to dealing with plastic waste,” she said in a statement.
But ACC said the chemical recycling industry has crunched the numbers on how such technologies “can help dramatically reduce the amount of waste sent to landfills while generating a diverse range of marketable products.” About 24.5 million metric tons of plastics were landfilled in the United States in 2018, according to the EPA. ACC calculates that about half of that — 12 million metric tons a year — would be considered “recoverable plastics” that chemical recycling facilities could use as feedstock once such facilities are up to scale.
The chemical recycling industry has tried to make clear that many methods of chemical recycling are not done using burning or high heat, but groups like the Natural Resources Defense Council maintain that many types of chemical recycling are simply incineration and don’t result in new products. GAIA, meanwhile, pushed back against Dow’s recent chemical recycling projects, citing an investigation by Reuters that said one of the programs Dow created to collect “hard-to-recycle” plastics for chemical recycling was actually sending the materials to a cement kiln.
NRDC also maintains that most techniques, including ones that use solvents or chemical depolymerization methods, create hazardous waste. NRDC and other environmentalists take issue with chemical recycling facilities choosing facility sites located in poorer communities or places with a predominantly minority population.
Some mechanical recyclers have also spoken out against chemical recycling projects, including the Alliance of Mission-Based Recyclers, a group of nonprofit MRFs. The group says companies that market chemical recycling projects as a solution for managing low-value or “problematic” plastics are overselling their abilities.
"The end goals of any plastics recycling should be to reduce reliance on virgin fossil fuels and support a circular economy," said Lynn Hoffman, National Coordinator for AMBR and Co-President of Eureka Recycling, in a statement. "Every recycling system should be evaluated based on its ability to meet these goals, and chemical recycling fails the test."
At this stage in chemical recycling’s lifecycle, there isn’t much data that can shed additional insight on claims from either side. That’s partly because so few facilities are running at scale, and because efforts to study the technologies’ environmental impact have so far come from grassroots advocacy groups and haven't gained widespread backing from agencies like the EPA.
The technologies are only becoming more widespread, but could be several years before chemical recycling’s business case — and its impact on the environment and recycling streams — becomes more clear.
Stay tuned for Part 2, which will take a look at the current markets and movement of materials chemical recycling companies are purchasing, as well as the role of MRFs and other processors in the material chain.